

Fault D may be caused by a flaw in the insulation or the result of a weak spot in the insulation that is aggravated by the presence of moisture. This condensation may completely evaporate during engine operation, but the carbon track that is formed by the initial flashover remains to allow continued flashover whenever high manifold pressure exists. Fault C is the result of condensation collecting in the lowest portion of the ignition manifold.
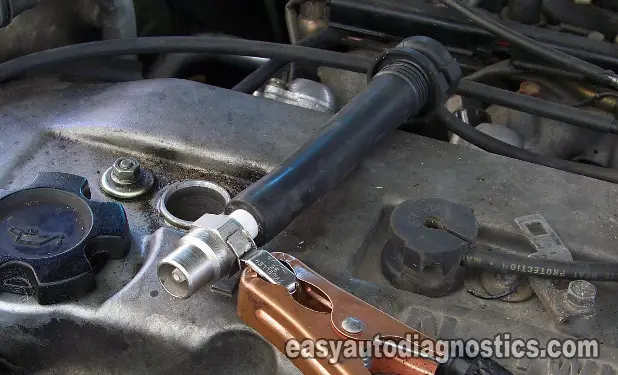
Although the insulation is not completely broken down, more than normal leakage exists, and the spark plug to which this cable is connected may be lost during takeoff when the manifold pressure is quite high.

Fault B illustrates a cable with a portion of its insulation scuffed away. This fault usually causes misfiring, since the spark is short circuited to a plug in a cylinder where the cylinder pressure is low. Fault A shows a short from one cable conductor to another. įigure 16 demonstrates four faults that may occur. After a spark plug has been seated with the fingers, use a torque wrench and tighten to the specified torque. As the shell stretches, the seal between the shell and core insulator is opened, creating a loss of gas tightness or damage to the core insulator. Shell stretching occurs as excessive torque continues to screw the lower end of the shell into the cylinder after the upper end has been stopped by the gasket shoulder. The use of excessive torque might compress the gasket out of shape and distort and stretch the plug shell to a point where breakage would result during the next removal or installation.
TESTING SPARK PLUG INSTALL
If a high torque is needed to install the plug, dirty or damaged threads on either the plug or plug bushing are indicated. In this case, only a small amount of additional tightening torque is needed to compress the gasket to form a gastight seal. If you can screw the plug into the cylinder with comparative ease using your fingers, this indicates good, clean threads. To install a spark plug, start it into the cylinder without using a wrench of any kind, and turn it until the spark plug is seated on the gasket. Replace the cylinder if, during the thread-cleaning process, the bushing is found to be loose, loosened in the cylinder, or the threads are cross-threaded or otherwise seriously damaged. This removes carbon deposits from the bushing threads without removing bushing metal, unless the pitch diameter of the threads has contracted as the result of shrinkage or some other unusual condition.
TESTING SPARK PLUG FULL
When screwing the tap into the bushing, be sure that the full tap cutting thread reaches the bottom thread of the bushing. To start the tap on installations where the spark plug hole is located deeper than can be reached by a clenched hand, it may be necessary to use a short length of hose slipped over the square end of the tap to act as an extension. Align the tap with the bushing threads by sight where possible, and start the tap by hand until there is no possibility of it being cross-threaded in the bushing. Before inserting the cleanout tap in the spark plug hole, fill the flutes of the tap, or channels between threads, with clean grease to prevent hard carbon or other material removed by the tap from dropping into the inside of the cylinder. If the firing pattern is good, the plug should be returned to its holder ready for installation in the engine.īrass or stainless steel spark plug bushings are usually cleaned with a spark plug bushing cleanout tap. As this test takes place, the firing end of the plug is subjected to air pressure to simulate the pressure in the engine’s cylinder. The spark plug should be tested by using a tester as shown in Figure 8, which passes a high-voltage through the spark plug and fire the gap. If the plug passes the firing end visual and cleaning checks, then the spark gap should be set using a round thickness gauge. The firing end should be inspected using a light and a magnifying glass. The shielding barrel insulators may be cleaned with a cotton cloth or felt swab saturated with solvent, wood alcohol, or other approved cleaner. After the abrasive blast, the firing end gets a thorough air blast to remove the abrasive material. As the firing end is subjected to the abrasive blast, the plug should be rotated so all the area of the firing end is cleaned.

This is usually done using a spark plug cleaner tester.
